
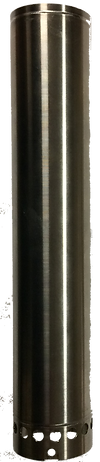
Titanium welded Dewar flask.
Made to customers specification and dimensions. Used in borehole seismic equipment to improve working time of electronic payload at elevated temperatures.

Customer relations are central to our business model at EBE Ltd. Proud of our reputation, we consistently meet the needs of our existing customer base and welcome the requirements of new customers.
EBE Ltd have customers in various industries, these include;
-
Autosport
-
Gear and Drive Train manufacturers
-
Oil and Gas
-
Geological sensors
-
Pressure Sensors
-
Gas analytical probes
-
Automotive Gears and transmission
-
Pneumatic Valves / solenoids
-
Dewar Flasks
-
Food processing equipment
Who uses Electron Beam welding?

Eb welding Synchro rings on to
automotive gears gives a high integrity welded joint with minimal
distortion and post weld machining. The process is highly repeatable therefore lending its self to batch work
Electron beam weld v TIG weld

316L stainless steel pipe.
42mm OD x 6.35mm wall thickness.
Eb weld; no joint prep, 760mm/min weld speed, 10 second weld time, single pass.
TIG weld; 45° vee prep. 200mm/min weld speed, multi pass, 20 minute + weld time.
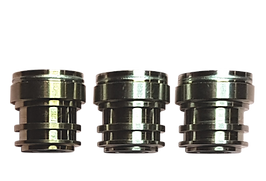
Electron beam welding is an ideal process for the joining of sensitive diaphragms used in the sensor industry due to it's low heat input and fast welding speeds.

Plant list;
-
Eb welder 9”(220mm) cube chamber
-
Eb welder 12”(300mm) cube chamber
-
Eb welder 4” dia tube chamber
-
3D systems 3500HD Max 3D printer
-
Leybold PheoniX L 300 mass spectrometer
-
XYZ 425 Proturn lathe
-
Miller Dynasty 200 Ac/Dc Tig Set
The precise control of the Electron beam welding process enables the smallest components to be successfully welded.
-
Pros.
-
Fast welding speeds
-
Minimal joint prep
-
High quality welds
-
Parts welded in a vacuum atmosphere
-
Minimal post weld machining
-
Cons.
-
Cannot be welded on site
-
Expensive welding equipment
-
Size of vacuum chamber determines size of parts to be welded